4.4.2.1. Surface Corrosion
Surface corrosion appears as a general roughening, etching, or pitting of the surface of a metal, frequently accompanied by a powdery deposit of corrosion products.
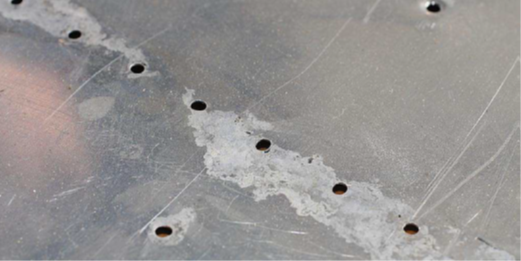

Surface corrosion may be caused by either direct chemical or electrochemical attack. Sometimes corrosion will spread under the surface coating and cannot be recognized by either the roughening of the surface or the powdery deposit. Instead, closer inspection will reveal the paint or plating is lifted off the surface in small blisters which result from the pressure of the underlying accumulation of corrosion products.
Filiform corrosion gives the appearance of a series of small worms under the paint surface. It is often seen on surfaces that have been improperly chemically treated prior to painting.
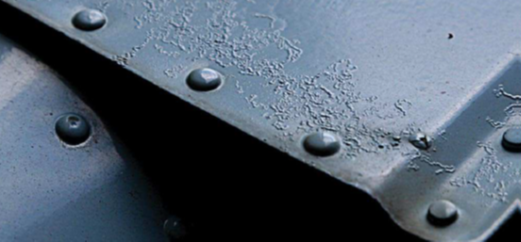

4.4.2.2. Galvanic or Dissimilar Metal Corrosion
Extensive pitting damage may result from contact between dissimilar metal parts in the presence of a conductor. While surface corrosion may or may not be taking place, a galvanic action, not unlike electroplating, occurs at the points or areas of contact where the insulation between the surfaces has broken down or been omitted. This electrochemical attack can be very serious because in many instances the action is taking place out of sight, and the only way to detect it prior to structural failure is by disassembly and inspection.
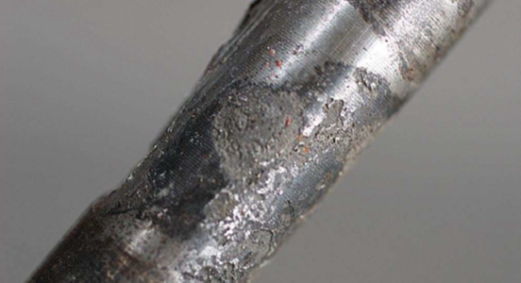

The contamination of a metal’s surface by mechanical means can also induce dissimilar metal corrosion.
The improper use of steel cleaning products, such as steel wool or a steel wire brush on aluminum or magnesium, can force small pieces of steel into the metal being cleaned, which will then further corrode and ruin the adjoining surface. Carefully monitor the use of nonwoven abrasive pads, so that pads used on one type of metal are not used again on a different metal surface.
Galvanic corrosion is covered in greater depth in section 4.4.5.
4.4.2.3. Intergranular Corrosion
This type of corrosion is an attack along the grain boundaries of an alloy and commonly results from a lack of uniformity in the alloy structure. Aluminum alloys and some stainless steels are particularly susceptible to this form of electrochemical attack. The lack of uniformity is caused by changes that occur in the alloy during heating and cooling during the material’s manufacturing process. Intergranular corrosion may exist without visible surface evidence.
Very severe intergranular corrosion may sometimes cause the surface of a metal to “exfoliate.” This is a lifting or flaking of the metal at the surface due to delamination of the grain boundaries caused by the pressure of corrosion residual product buildup. This type of corrosion is difficult to detect in its initial stage. Extruded components such as spars can be subject to this type of corrosion. Ultrasonic and eddy current inspection methods are being used with a great deal of success.
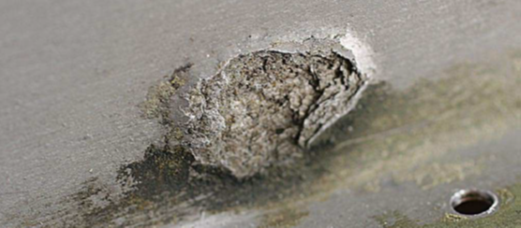

4.4.2.4. Stress Corrosion
Stress corrosion occurs as the result of the combined effect of sustained tensile stresses and a corrosive environment. Stress corrosion cracking is found in most metal systems; however, it is particularly characteristic of aluminum, copper, certain stainless steels, and high strength alloy steels (over 240,000 psi).
It usually occurs along lines of cold working and may be transgranular or intergranular in nature. Aluminum alloy bellcranks with pressed in bushings, landing gear shock struts with pipe thread type grease fittings, clevis pin joints, shrink fits, and overstressed tubing B-nuts are examples of parts which are susceptible to stress corrosion cracking.
Stress Corrosion is covered in greater depth in section 4.4.7.
4.4.2.5. Fretting Corrosion
Fretting corrosion is a particularly damaging form of corrosive attack that occurs when two mating surfaces, normally at rest with respect to one another, are subject to slight relative motion.
It is characterized by pitting of the surfaces and the generation of considerable quantities of finely divided debris. Since the restricted movements of the two surfaces prevent the debris from escaping very easily, an extremely localized abrasion occurs. The presence of water vapor greatly increases this type of deterioration.
If the contact areas are small and sharp, deep grooves resembling brinell markings or pressure indentations may be worn in the rubbing surface. As a result, this type of corrosion (on bearing surfaces) has also been called false brinelling.
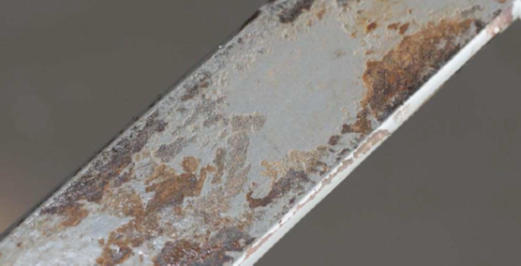
