In general, welded aluminum is not used for certified aircraft primary structure. This is due to concerns over meeting quality requirements with regard to weld porosity and the resulting fatigue life. Welded aluminum is commonly used for secondary structure and some systems applications.
The availability of data for the strength of welded aluminum is limited. The following data is compiled from several sources.
12.5.3.1. Strength of Welded 2000 Series Aluminum
This data is derived for a 2219 aluminum Panel TIG welded to a 2219 aluminum forging and heat treated to the T87 condition. The following results are based on the average of 24 specimens.
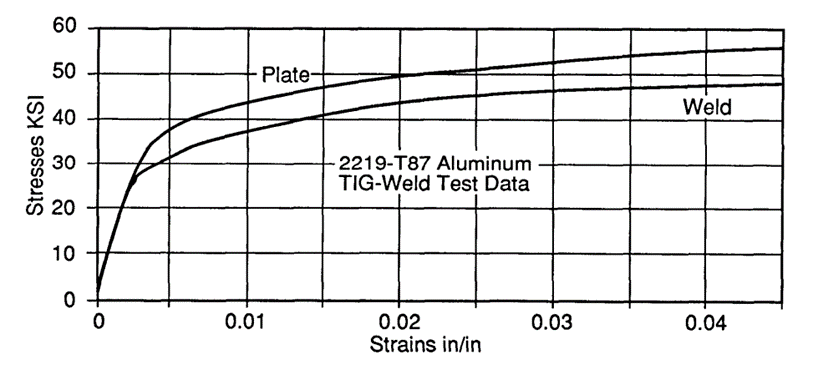

This data is average (and not A or B basis) but does give a good indication of the reduction in strength. This reduction in strength can be considered to apply to the available statistical basis material data.
In addition, NASA gives the following guidance for minimum ultimate tensile strength of butt welds (NASA-CR-2064, 1972):
Alloy 2219-T87, Minimum UTS = 35000 psi
Alloy 2014-T6, Minimum UTS = 38000 psi
12.5.3.2. General Guidance for the Strength of Welded 5000 and 6000 series Aluminums
5000 series aluminum is work hardened and cannot be heat treated. Therefore, the immediate post weld strength of the 5000 series aluminum material cannot be improved upon.
(MIL-HNDBK-5H, 1998) has data for 5052 in the O condition and these values can be assumed to apply for 5052 aluminum in the welded state.
Fty = 9500 psi
Ftu = 25000 psi
6061 series aluminum can be heat treated post weld to increase strength. (NASA-CR-123772, 1972) gives good guidance on the correct approach and some useful strength data.
6061 should be procured in the T4 condition, welded and then aged to the T6 condition after welding.
