If the slenderness ratio of a column is low enough that some its fibers are no longer in the elastic range at the time of failure the Euler formula no longer holds. In this instance the tangent modulus can be used in place of the Young’s Modulus in the Euler equation:
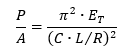
This produces results that are generally less conservative than the Johnson column allowable based on Fcy.
The effect of the tangent modulus on the buckling allowable can be derived analytically using the Ramberg-Osgood approximation for the plastic stress-strain curve.
In the authors experience, for typical isotropic structural materials, the effect of the shape factor rarely reduces the buckling allowable lower than that of the Johnson Buckling Curve:
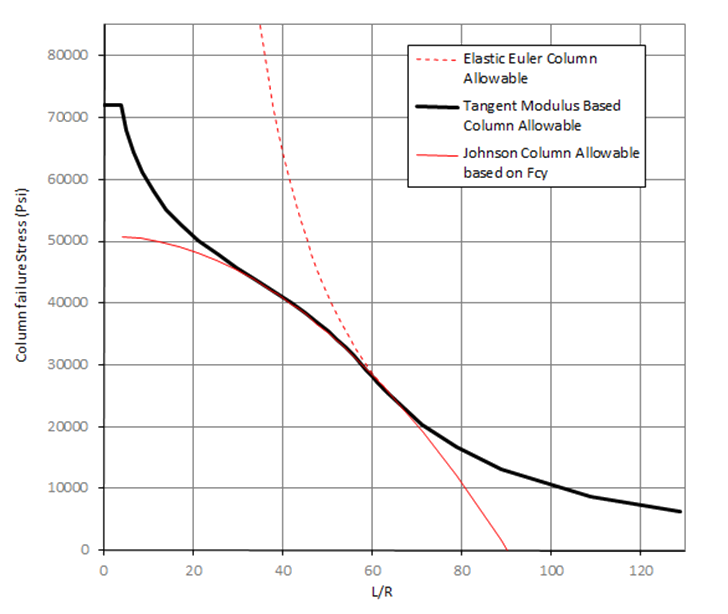
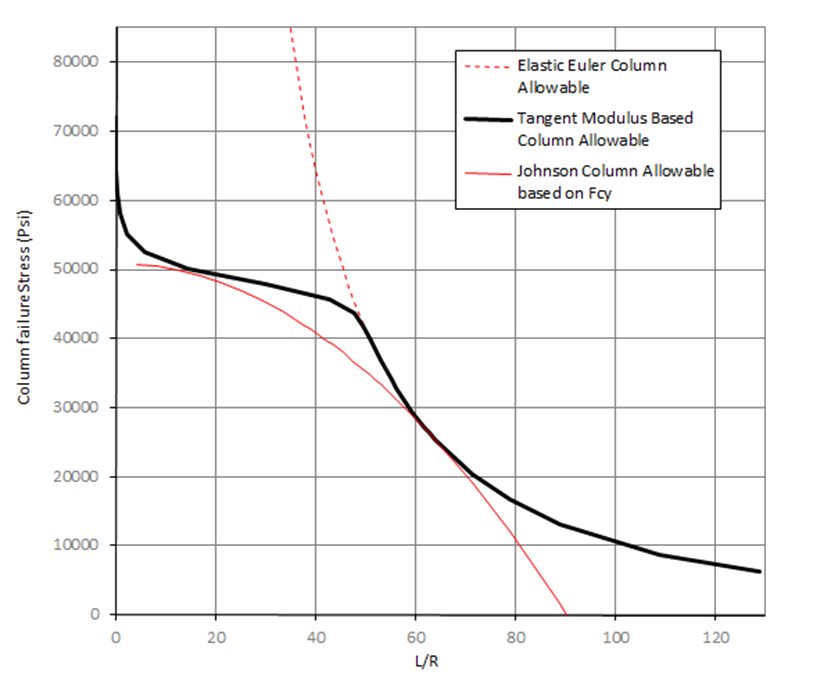
The figures above show that for a sample. Typical ductile material the tangent modulus curve with shape factors between 10 and 40 lie between the Euler and the Johnson Buckling Curves and do not exhibit a lower value than the Johnson Curve.
This implies that for inelastic columns with stable cross sections the Johnson curve can be used as a conservative sizing allowable.
For materials with very low shape factors (less than 10) it is advisable to carry out a full tangent modulus analysis.

Figure 15.3.4‑3 shows that a ductile material with a shape factor of 5 exhibits column strength significantly lower over a significant slenderness ratio range than the Johnson Buckling Curve. This method is covered in the following spreadsheet: