The monocoque (single shell) fuselage relies largely on the strength of the skin or covering to carry the primary loads.
The design may be divided into two classes:
1. Monocoque
2. Semi monocoque
Different portions of the same fuselage may belong to either of the two classes, but most modern aircraft are of semi monocoque type construction.
22.12.2.1. True Monocoque Type
A true monocoque construction uses formers, frame assemblies, and bulkheads to give shape to the fuselage, reference Figure 22.12.2‑1. The heaviest of these structural members are located at intervals to carry concentrated loads and at points where fittings are used to attach other units such as wings, powerplants, and stabilizers. Since no other bracing members are present, the skin must carry the primary stresses and keep the fuselage rigid. Thus, the biggest problem involved in monocoque construction is maintaining enough strength while keeping the weight within allowable limits.
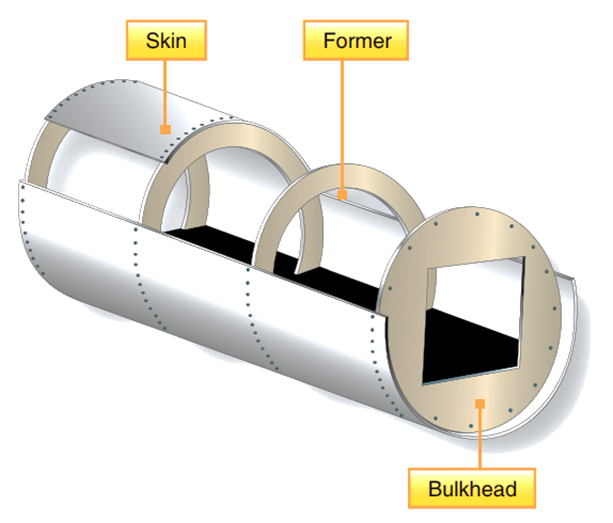

22.12.2.2. Semi monocoque Type
To overcome the strength/weight problem of monocoque construction, a modification called semi monocoque construction was developed. It also consists of frame assemblies, bulkheads, and formers as used in the monocoque design but, additionally, the skin is reinforced by longitudinal members called longerons.
Longerons usually extend across several frame members and help the skin support primary bending loads. They are typically made of aluminum alloy either of a single piece or a built-up construction. Stringers are also used in the semi monocoque fuselage.
These longitudinal members are typically more numerous and lighter in weight than the longerons. They come in a variety of shapes and are usually made from single piece aluminum alloy extrusions or formed aluminum. Stringers have some rigidity but are chiefly used for giving shape and for attachment of the skin. Stringers, longerons and the skin resist fuselage bending.
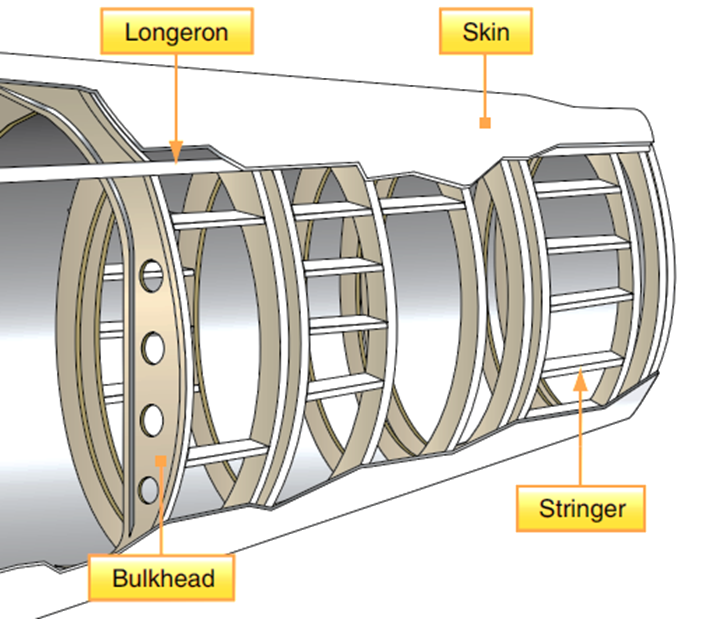

Other bracing between the longerons and stringers can also be used. Often referred to as web members, these additional support pieces may be installed vertically or diagonally. It must be noted that manufacturers use different nomenclature to describe structural members. For example, there is often little difference between some rings, frames, and formers.
The semi monocoque fuselage is constructed primarily of alloys of aluminum and magnesium, although steel and titanium are sometimes found in areas of high temperatures. Individually, no one of the components is strong enough to carry the loads imposed during flight and landing. But, when combined, those components form a strong, rigid framework. This is accomplished with gussets, rivets, nuts and bolts, screws, and even friction stir welding. A gusset is a type of connection bracket that adds strength.
For semi monocoque structure made from aluminum the skin panels can be allowed to buckle above normal service loads. The longeron and stringers give adequate residual strength in the post buckled state. This design approach allows thin skin panels and generally produces the lightest weight structure.
Composite fuselage construction can be without any frames at all (relying on core to give the skin adequate stiffness), with frames or with frames, stringers and longerons, known as black metal as the design is very similar to semi-monocoque metal fuselage design but the carbon material gives it a black color. It is unusual to allow composite primary structure to buckle, therefore composite structure generally exhibits linear behavior up to ultimate load.