NASA-TM-2012-217454
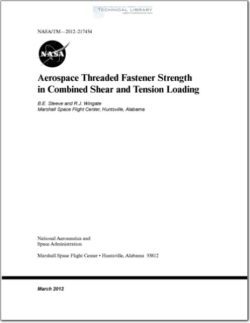
- Version
- 3059 Downloads
- 4.95 MB File Size
- 1 File Count
- November 27, 2015 Create Date
- June 4, 2019 Last Updated
Fastener Strength In Combined Shear And Tension Loading
The strength capability of aerospace threaded fasteners is typically specified as a minimum
tensile strength or minimum double shear strength in either a standard part or procurement speci-
fication. These values are usually derived by multiplying the thread tensile stress area by the design
allowable ultimate tensile stress of the fastener material or by multiplying the area of the full diam-
eter body (herein referred to as the body) by the design allowable ultimate shear stress, respectively.
Acceptance testing is performed on manufacturing lots to verify that each lot of bolts is at least as
strong as the minimum specification values.
The specification strength values are only applicable to fasteners that are loaded in either
pure tension or pure shear. For bolted joints that do not have a design feature to react applied shear
loads, the bolts are required to carry a combination of shear and tension loading. Load interac-
tion failure criteria exist for members in combined shear and tension loading,l including a com-
monly used criterion specifically for threaded fastenersHl However, a survey of literature reveals
that there is little data available to validate these failure criteria for aerospace bolts in a typical
preloaded joint installation. Furthermore, these existing failure criteria are intended for instances
where the shear plane is at a smooth, constant cross section and do not necessarily apply to
a threaded fastener with the shear plane through the threads.
A test program was initiated by Marshall Space Flight Center and sponsored by the NASA
Engineering and Safety Center to validate existing combined loading failure criteria and to quan-
tify the effect of threads in the shear plane. The testing consisted of a series of 46 tests of indi-
vidual bolts. The bolts were loaded to failure at several angles relative to the bolt axis, similar to
test method MIL-STD-l312-2,5 using a custom designed test fixture. The testing included a group of
fasteners with the shear plane passing through the full diameter body and a group of fasteners with the
shear plane passing through the threads. Both of these groups were further divided into fasteners that
were installed with zero preload and fasteners that were installed with a high initial preload. Table 1 lists
the complete test matrix.
File | Action |
---|---|
NASA-TM-2012-217454-Fastener-Strength-in-Combined-Shear-and-Tension-Loading.pdf | Download |
Comment On This Post