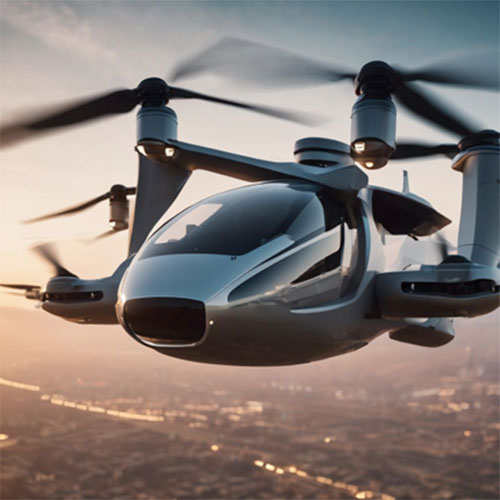
This is an early draft of the first section of three sections – spit into technical, commercial and compliance – non referenced images are all AI generated.
Almost every eVTOL aircraft is based on an electrical distributed propulsion architecture. Typically, this is in the form of multiple propellers or rotors driven by multiple electric motors. This type of configuration is only possible with electric drive systems. Turbine or piston engines generally must be ‘in line’ with the propeller or thrust vector (this is not the case for helicopters where heavy, expensive and complex gear boxes are required). Turbine and propeller engines do not scale efficiently below a certain level and require complex mounting and fuel system arrangements. This makes piston and turbine engines inherently unsuitable for a distributed propulsion architecture that requires many small motors driving multiple rotors or propellers.
There is an old dictum in aircraft design – you design the aircraft around the engine. When your engine is new and unique the risk of technical failure is high. The aircraft is designed around a major system that is unique and there is no replacement.
If an electrical drive system in an eVTOL aircraft design is flawed for any reason it is very likely there are no similar and suitable alternative powertrain systems. These air vehicles that use distributed propulsion cannot be converted to traditional drive systems. These air vehicles are rendered useless and worthless.
This is why almost all conventional aircraft programs have an ‘A’ primary powerplant choice and an alternative ‘B’ engine that they can use with some adaptation. If your engine supplier lets down an OEM, they need a way to continue with their program and recoup the investment.
What are the technical risks inherent in a typical eVTOL power train?
There are two major risks that affect the technical and market viability of an electric powertrain.
Batteries
Batteries are a suitable energy storage medium in non-weight critical applications where low power output is required. Laptops, phones, flashlights, etc.
Batteries have low energy density compared to hydrocarbon liquid fuels[1]. This can be seen in the limited published range and endurance numbers published for eVTOL and other electrical aircraft. The image below shows the effect of converting a helicopter to a battery powered electric drive system[2].
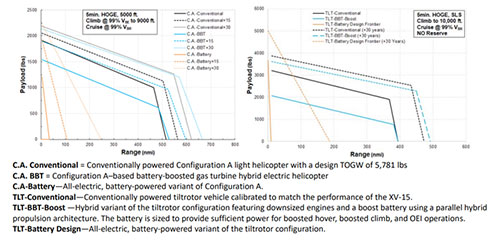
With contemporary battery technology the range of a conventional helicopter is reduced by a factor of more than ten. With projected battery technology in thirty years’ time, the range is still less than half of a conventional helicopter today.
Modern batteries (lithium polymer) have an irreversible thermal failure mode that results in temperatures about twice that of burning aviation fuel and are effectively inextinguishable as burning batteries generate their own oxygen for the combustion process.[3]
This critical failure mode of batteries and the requirement for residual power for safe flight and landing after any failure creates additional system complexity and additional weight. Battery installations must be designed with a high degree of redundancy, separation, venting and thermal protection.[4]
The weight of these risk mitigations further degrades the already low performance of the aircraft.
Motor Certification
It is not widely known but as of writing there is no electric motor that is certified for commercial aircraft primary powertrain use. There is one motor that is certified for use in Light Sport Aircraft. This is the Pipistrel Velis powertrain[5]. There are several projects that may result in a certified aircraft electric drive system such as SAFRAN[6] who aim to have their motor certified by first quarter 2024, Rolls Royce[7] (who bought the business from Siemens[8]) who again target 2024 for certification and MagniX[9]. MagniX probably has the longest development program, having started in 2009 and they have not published a date for certification.
There will be a limited and uncertain choice of electric motors for eVTOL developers to choose from. However, vehicles have already been configured, developed, flown and certification programs have begun.
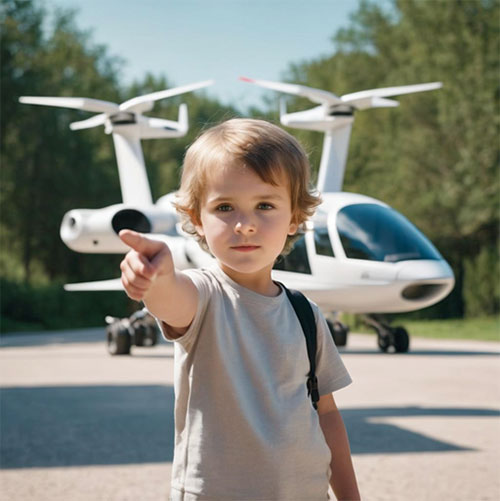
This is similar to running the first leg of a relay race while your teammates are at the sports store working out if they can afford to buy a pair of running shoes.
Certification of a new aircraft system does not guarantee reliability of that system in service conditions. Almost all complex systems when they are first put into service suffer from lower than planned reliability. Electric aircraft powertrains will be no different.
Other Powertrain Systems
There is a plethora of positive messaging and targeted investments for hydrogen powered aircraft. Hydrogen has a wide range of practical barriers in the way of aircraft powertrain applications. This subject will not be covered in depth here, but some of the more significant problems around hydrogen as a fuel are: Availability, delivery, ground storage and handling, refueling, storage on the aircraft (very low temperature, high pressure, off gassing and the inability to store on the aircraft for anything other than the very short term), the volume required to store the gas, the immaturity of hydrogen fuel cell technology and hydrogen embrittlement of storage and distribution (on and off the aircraft) and powertrain components.
Control Systems
Almost all eVTOL aircraft lack any form of natural aerodynamic stability. This is a fundamental difference compared to helicopters and fixed wing aircraft.
Helicopters have no stick free stability and always require active pilot input. They are stable enough that they do not require software control system to fly.
eVTOL aircraft require stabilizing software similar to quad copters and other small UAVs. This type of vehicle stabilizing software has not been used for any manned aircraft or been certified before.
Manned aircraft approaching this low level of natural stability have only ever been developed for military applications. The level of aerodynamic stability for military applications is still maintained at the highest level possible considering the required mission envelope.
The technical risk of the control system for most eVTOL exceeds that of a $40Bn[10] military development program. This is not to suggest that it will cost this amount of money to develop and certify an eVTOL control system.
However, it is true to say that the technical risk for eVTOL control systems is greater than that accepted by large military programs with very high budgets.
Technical Summary
It is normal for aircraft developers to minimize technical risk to those areas that are absolutely required for the required incremental commercial improvement to justify the investment necessary for a new product.
eVTOL OEMs have adopted a new paradigm of accepting very high technical risks and spending very large amounts of money to mature new systems and attempt adequate risk mitigation.
This approach is diametrically opposed to that which has been consistently successful.
- https://en.wikipedia.org/wiki/Energy_density
- https://ntrs.nasa.gov/api/citations/20205000636/downloads/2021-08-20-eVTOL-White-Paper-Final_V48.pdf
- https://www.sciencedirect.com/science/article/pii/S2542435118302800
- https://www.easa.europa.eu/downloads/136701/en
- https://www.pipistrel-aircraft.com/products/velis-electro/
- https://www.safran-group.com/products-services/engineustm
- https://www.rolls-royce.com/products-and-services/electrical/our-electrical-power-and-propulsion-portfolio.aspx
- https://press.siemens.com/global/en/pressrelease/siemens-sells-electric-aircraft-propulsion-business-rolls-royce
- https://www.magnix.aero/
- https://en.wikipedia.org/wiki/Lockheed_Martin_F-35_Lightning_II_procurement
Thank you
Hi Richard,
Your analysis is tremendously true. As aeronautical engineer I feel really uncomfortable with this financial driven approach to the projects. But this train is running and I don’t know how to reduce the “impact” velocity!!!
For your info: among the OEM who are certifying an EPS there is also H55 (https://h55.ch/technology/#technologyHeader); the TC is expected in 2024, they say.
I think engineers (and engineeing leadership) need to speak up more. As a recovering stress engineer (and recovering parent) I am used to saying no to all kinds of people at all levels. There are mnay ways to say no and we need to get better at it. It is hard when paying your mortgage depends on being part of the team…….but we need to take the pain in the short term to create a viable long term. The destruction of capital coming up will make the VLJ bubble look like an amateur side show.