NASA-TM-210844
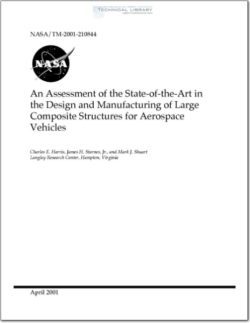
- Version
- 187 Downloads
- 2.69 MB File Size
- 1 File Count
- December 13, 2015 Create Date
- December 13, 2015 Last Updated
Assessment of the Design and Manufacturing of Large Composite Aerospace Vehicles
An assessment of the design and manufacturing practices for large composite structures
has been conducted to determine the current state-of—the—art for these technologies. The
background that motivated the assessment was a series of unexpected manufacturing and design
problems with the composite structures of several NASA experimental vehicles currently under
development. The focus of the assessment is on the use of polymeric matrix composite materials
for large airframe structural components such as those in commercial and military aircraft and
space transportation vehicles. The baseline for the assessment is the historical evolution of the
use of composite materials in actual aerospace vehicles. The assessment emphasizes the
application of composite structures in moderately to heavily loaded aerospace vehicles.
Applications of composite materials are reviewed for large commercial transport aircraft, general
aviation aircraft, rotorcraft, military fighter aircraft, and military transport aircraft. The baseline
also includes the application of composite materials for unmanned rockets and space
transportation vehicles. The assessment of the state-of—the-art includes a summary of lessons
learned, examples of current practice, and an assessment of advanced technologies under
development. The assessment concludes with an evaluation of the future technology challenges
associated with applications of composite materials to the primary structure of commercial
aircraft and advanced space transportation vehicles.
As a preamble to assessing the state-of—the-art in the design and manufacturing of
composite structures, the design requirements for aerospace vehicles are briefly reviewed.
Because of the universal design requirement to minimize the gross take-off weight of all
aerospace vehicles, aerospace structural components are designed at or near zero margin of
safety. While the margin of safety is not equal to zero for all the design criteria at each structural
location, there is typically one criterion for each structural element that governs the design
details of that element. The quest for the lowest weight structure then drives the design margin
to nearly zero for the design limit load condition. (The Code of Federal Regulations [1] for
Aeronautics and Space, Title 14, specifies that the structure shall undergo no permanent
deformation at the design limit load (DLL). In addition, the structure shall sustain the design
ultimate load (DUL) for at least 3 seconds before failing.
File | Action |
---|---|
NASA-TM-210844 Assessment of the Design and Manufacturing of Large Composite Aerospace Vehicles.pdf | Download |
Comment On This Post