NASA-CR-2010-216700
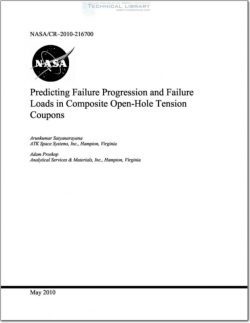
- Version
- 309 Downloads
- 10.54 MB File Size
- 1 File Count
- June 15, 2016 Create Date
- June 15, 2016 Last Updated
Predicting Failure Progression and Failure Loads in Composite Open-Hole Tension Compounds
Abstract
Failure types and failure loads in carbon-epoxy [45/90/45/0Jms
laminate coupons with central circular holes subjected to tensile load
are simulated using progressive failure analysis (PFA) methodology.
The progressive failure methodology is implemented using VUAMT
subroutine within the ABAQUSTM/Explicit nonlinear finite element code.
The degradation model adopted in the present PFA methodology uses an
instantaneous complete stress reduction (COST R) approach to simulate
damage at a material point when failure occurs. In-plane modeling
parameters such as element size and shape are held constant in the finite
element models, irrespective of laminate thickness and hole size, to
predict failure loads and failure progression. Comparison to published
test data indicates that this methodology accurately simulates brittle,
pull-out and delamination failure types. The sensitivity of the failure
progression and the failure load to analytical loading rates and solvers’
precision is demonstrated.
1.0 Introduction
Use of composite laminates in primary aerospace structures is rapidly increasing due to their high
strength, low weight, ability to manufacture complex geometries and other factors. The strength and
failure type of composite laminates are essential information required by engineers to design structures to
meet safety requirements. Of particular interest are structural components with discontinuities (e.g.,
cutouts, holes, etc.). Over the past several years many researchers have embarked on developing
progressive failure analysis (PFA) methodologies to predict failure loads and damage modes in
composites [1—23]. However, the reliability of these methodologies in analyzing typical aerospace
structural components needs to be improved.
The PFA methodology development is a complex task resulting in significant challenges at
several steps of the procedure. One such step, which is also an active research area in PFA methodology
development, is defining degradation models for adjusting material properties or stresses to simulate
damage modes such as fiber, matrix and inter-laminar (delamination) failures. Identifying material
properties or stresses to degrade for the given damage modes, and the rates of degradation themselves, are
all part of ongoing research. The PFA methodologies and the damage models which are commonly used
to predict the in-plane damage modes and the failure loads are very well summarized in Refs. 1, and 13.
Most of the in—plane damage models are successful in predicting fiber and matrix failure in most laminate
sequences where the through-thickness crack propagates in a self-similar fashion (i.e., perpendicular to
the loading direction). Another factor which makes the PFA methodology less reliable is its dependency
on the element size for accurate solution predictions. Dependency of the failure load predictions on the
element size is a well known phenomenon. Researchers in Refs. 13—14 attempted to address this issue by
equating the fracture energy of the material to the energy dissipation due to the damage mode. As
indicated in Ref. 14, fracture properties of the fiber may not be as readily available as other standard
material properties.
To compensate for the lack of maturity of PFA methodology and also to generate test data to
support its development and validation efforts, several experimental investigations were conducted in the
recent past. Among test results published in the literature, Green et al. [24] reported on their tests
conducted on the composite tension coupons with a centrally located hole. Three distinct failure types
were observed in the test. Based on the post-failure examination of the specimens, the failure types were
characterized as brittle, pull-out and delamination, and were shown to be dependent upon the diameter of
the hole, the laminate thickness and the stacking sequence. These unique failure types were triggered by
one of the in-plane stresses reaching the failure limit ahead of the others. Since the test results published
by Green at al. [24] covered all the three known failure types, they were selected as an attractive and
comprehensive ground for the validation effort of the PFA methodology used in the current study.
The objective of the current work was to examine the capabilities of the previously developed in-
plane damage models [12, 19] and the modeling procedures in predicting the failure load and the failure
types of the open-hole tension specimens. Simulation of complex failure types, such as the ones shown in
the experimental work by Green et al. [24], requires both intra-laminar and inter-laminar damage models
applied simultaneously. This is a challenging task that tests the limits of the damage models. The
detection of intra-laminar damage was accomplished using the Hashin-Rotem failure criteria [25—27].
The intra-laminar modeling parameters, such as the in-plane mesh size and its orientation around the
discontinuous regions, were maintained approximately constant for all the coupons analyzed in this study
and are described in the finite element model development section. The explanation of the degradation
technique and the damage model used in the current study are presented in the following sections. The
damage model with failure criteria for PFA was implemented using user-written material modeling
subroutine (VUMAT) in the ABAQUSTM finite element analysis code and its explicit nonlinear solver
was used in the simulation. The inter-laminar damage mode (delamination) was simulated using cohesive
zone model [28—30] in ABAQUSTM. The inter-laminar modeling procedure for the cohesive layers is
explained in the finite element model development section of this report.
In the current study, PFAs of 8-, l6— and 32-ply laminates with a 0.25-inch and 0.5-inch—diameter
hole located at the center were performed. A 32-ply laminate with a 0.5-inch-diameter hole located at the
center, but scaled in such a way as to not group same-direction plies together, was also analyzed. Results
such as failure loads and the failure types of these laminates obtained from the PFA are presented in
tabular and pictorial forms showing the inter-laminar and the intra-laminar damage modes and their
corresponding loads. Numerical results, such as failure stress, are compared with the test data provided
in Ref. 24. The detailed description of the failure types exhibited by these laminates, as explained in
Ref. 24, is compared with the simulated solutions obtained from the PFA.
In this study, the ABAQUSTM/Explicit solver was used to solve a dynamic equation of motion.
As application of very slow experimental loading rates of the coupons is impractical in the explicit
analysis, an accelerated loading rate was applied. Therefore, the loading rate of the coupons in the
analysis became an important factor. As a result, the influence of the loading rate and the application of
ABAQUSTM/Explicit single versus double precision solvers on the failure load, the failure types, and the
sub-critical damages around the notch were examined.
File | Action |
---|---|
NASA-CR-2010-216700 Predicting Failure Progression and Failure Loads in Composite Open-Hole Tension Compounds.pdf | Download |
Comment On This Post