AGARD-R-795
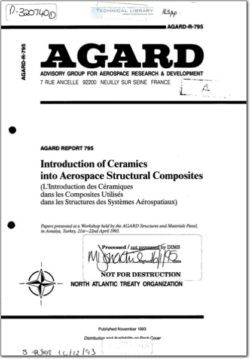
- Version
- 228 Downloads
- 47.64 MB File Size
- 1 File Count
- April 28, 2016 Create Date
- April 28, 2016 Last Updated
Introduction of Ceramics into Aerospace Structural Composites
During the last decade, Ceramic Matrix Composites
(CMC) have undergone a rapid development, so that
quite a number of composites are available today.
The best known SiC/SiC and C/SiC processed by the
Chemical Vapour Infiltration technique are now
produced on an industrial scale. C/SiC composite
currently operates at temperature above 1600°C for
propulsion application on launchers and missiles;
other composites with oxide or silicon-nitride matrices
are under development.
The processing routes are moving from CVI to more
cost-effective processes such as sol-gel and polymer
precursor. These routes appear very promising since
they currently use the technologies already developed
for Organic Matrix Composites and carbon-carbon.
The real challenge for these materials today refers to
both the working temperature, which must overpass
1600°C and the environmental behaviour. To meet
these requirements, new fibres with an increased
thermal stability are under development.
Since the very first research work performed in the
early 80’s, Ceramic Matrix Composites (CMC’s) have
experienced an exceptional development throughout
the last decade. The reported increase of CMC’s use
mainly for the manufacture of missile and rocket-
.engine hot components has been driven by the
constant need to reduce their weight and to increase
their working temperatures.
Today, the question of using CMC’s on turbojet
engines is raised, with the double aim of reducing the
weight and increasing the thrust to improve the thrust
over weight ratio. It is worth mentionning that
actually, the cooling of the blades requires to remove
up to 12 % of the engine total airflow, thus reducing
the thrust by the same amount. The replacement of
heavily cooled metallic components by solid ceramic
parts appears as one of the ways of improving the
engine efficiency without increasing the hot stages
working temperature and therefore the NOx release.
However, to achieve this aim, the reliability of CMC’s
relative to the requirements of their use on civilian or
military engines has to be proved. That means that
CMC’s able to work at temperature higher than
1400°C for long terms (>10.000 hours) within an
oxydizing and corrosive environment must be
available. The purpose of this paper is to review
briefly the existing materials and processing
technologies, so as to highlight their limitations and
to present the future needs for CMC’s development.
File | Action |
---|---|
AGARD-R-795 Introduction of Ceramics into Aerospace Structural Composites.pdf | Download |
Comment On This Post