AGATE-C-GEN-3451-2
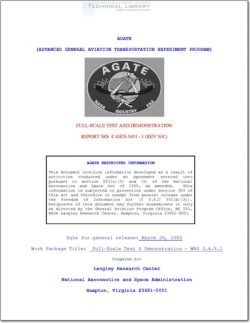
- Version
- 86 Downloads
- 2.62 MB File Size
- 1 File Count
- August 16, 2016 Create Date
- August 16, 2016 Last Updated
Full Scale Starship Drop Test
This report presents the results of Cessna’s crash
experiments conducted onboard the Beech Starship aircraft
fuselage. The test parameters were configured to attain the
impact requirements of FAR 23.562(b)(l) and (b)(2). The
aircraft was dropped from a vertical height of 50 feet and
followed a flight path of 27 degrees, resulting in an
vertical impact velocity of 29 fps and horizontal impact
velocity of 89 fps. The structural response of the
airframe, seats and ATD’s were measured throughout the test
and are presented in this report. The data collected and
analysis serves as a baseline study for improved
crashworthiness standards for general aviation commuter
airplanes.
The Starship full—scale drop test was conducted as part of
AGATE Workpackage W.B.S. 3.4.5.1 at the NASA Langley Drop
test Facility, Hampton Virginia in May 1998. The objective
of the test was to document and investigate the performance
of current (or ‘as-is’) sub-floor structures, seat and
restraint systems. This will provide a baseline for an
additional test with modified energy absorbing mechanism to
enhance occupant protection.
The Starship drop test airframe was supplied by Raytheon
Aircraft, which was configured to served as a platform for
a collective number of experiments conducted by Cessna
Aircraft, Simula Technologies, Impact Dynamics Inc.,
Aircraft Modular Products and Raytheon. This report
presents specifically the test results and analysis
pertaining to Cessna’s experiment onboard the Starship
airframe, and results of experiments conducted by other
workpackage members are not included.
Two Cessna’s experiments were conducted. One experiment was
to investigate the structural performance of an energy
absorbing seat structure that is subjected to a real—world
crash pulse. A second experiment investigates the
effectiveness of airbag systems to provide occupant
protection.
The Starship airframe is an all—composite structure. The
fuselage, frames and sub—floor structure is fabricated from
carbon fiber composite. For this test, ballast weights
were used to simulate engine masses, and the fuel cells
were filled with water to simulate fuel contents. Final
weight of the test article is 14,200 lbs.
File | Action |
---|---|
AGATE-C-GEN-3451-2 Full Scale Starship Drop Test.pdf | Download |
Comment On This Post