NASA-TP-2001-211302
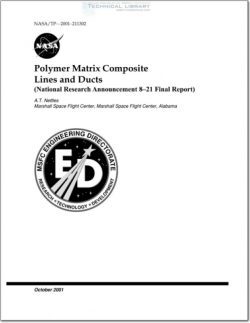
- Version
- 286 Downloads
- 12.92 MB File Size
- 1 File Count
- August 18, 2016 Create Date
- August 18, 2016 Last Updated
Polymer Matrix Composite Lines and Ducts
The Access—to—Space study identified the requirement for lightweight structures to achieve orbit
with a single—stage vehicle.1 The use of composite components is critical to fulfilling that requirement. The
purpose of this task is to extend previous efforts with polymer matrix composite (PMC) feedlines and
ducts.
This Technical Publication (TP) outlines the results of a task that was awarded under National
Research Announcement 8—21. This task is an element under the Reusable Launch Vehicle Focused Tech—
nology Project Plan. The task is titled “Polymer Matrix Composite (PMC) Lines and Ducts” and its main
objective was to demonstrate the feasibility of manufacturing a large diameter composite feedline with a
90° elbow section and integral flanges. Other objectives of the task were to demonstrate PMC performance
under cryogenic environments, to demonstrate knowledge of the damage tolerance issues associated with
composite feedlines, and to evaluate feedlines manufactured by four different techniques. To accomplish
these objectives, an 8—in.—diameter composite feedline for liquid hydrogen (LHZ) service was selected to be
designed because it is typical of those found in a launch vehicle main propulsion system.
While most feedline concepts currently use a metallic material, a small composite feedline was
successfully used on the Delta Clipper—Experimental Advanced flight vehicle. Larger feedlines of more
complexity need to be developed to realize even larger savings in weight. Typically, a composite feedline
can save over 50 percent mass to be manufactured via four different technologies: (1) Conventional hand
layup (HLU) and autoclave cure, (2) solvent—assisted resin transfer molding (SARTM), (3) electron beam
cure, and (4) thermoplastic tape laying (TTL).
NASA Marshall Space Flight Center (MSFC) was responsible for material selection and manufac—
ture of the feedlines made via the HLU method. NASA Glenn Research Center (GRC) was responsible for
material selection and manufacture of feedlines made by the SARTM process. Oak Ridge National
Laboratories (ORNL) was responsible for material selection and manufacture of feedlines to be made by
the electron beam cure process. Automated Dynamics Incorporated manufactured feedlines by TTL.
File | Action |
---|---|
NASA-TP-2001-211302 Polymer Matrix Composite Lines and Ducts.pdf | Download |
Comment On This Post