DSTO-TR-2773
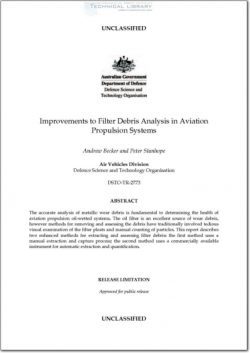
- Version
- 187 Downloads
- 5.28 MB File Size
- 1 File Count
- August 10, 2016 Create Date
- August 10, 2016 Last Updated
Improvements to Filter Debris Analysis in Aviation Propulsion Systems
The analysis of wear debris has been shown to be an effective condition monitoring tool
for oil-wetted systems and is considered to be a valuable adjunct to existing condition
monitoring techniques. The oil filter is a potentially rich source of information about the
health of oil—wetted components in aircraft machinery, but is generally under—utilised as a
condition monitoring tool in the Australian Defence Force. Historically, the analysis of
aircraft oil filter debris was time consuming and was not suited to in-field assessment. The
two primary challenges associated with oil filter analysis are extracting the debris in a
reliable and controlled manner and interpreting the debris to assess whether maintenance
action is required. In particular, the military context (involving regular deployments to
remote localities or to sea) presents its own set of challenges for extracting useful
information from oil filters. Additionally, the well documented benefits of introducing fine
oil filtration has resulted in some of the traditional oil analysis techniques, such as
Spectrometric Oil Analysis (SOA), becoming ineffective. In aviation propulsion machinery,
this generally leaves the filter and magnetic chip detectors as the prime sources of wear
debris information.
This report describes the application of two Defence Science and Technology Organisation
(DSTO) initiatives to improve the analysis of oil filter wear debris. The first initiative
involves the application of an in—field manual debris extraction kit to the F117—PW—100
engine (powering the C-17A aircraft) oil filters. The kit enables maintenance staff to
conveniently extract the filter debris and deposit it on a filter patch for inspection and
further analysis if required. The process used for extraction in this instance is a manual
method currently used on RAAF PC—9 / A aircraft. The previous method of inspecting the
filter from this engine involved visual inspection of each filter pleat and manual counting
of particles. The advantages of the new method include greater extraction efficiency (i.e.
greater recovery of debris compared to the previous method) and a less tedious and
laborious task for staff.
The second initiative involves the assessment, trial and introduction of a commercial
instrument known as FilterCHECK. This device automatically extracts the filter debris
using a combination of reverse fluid flow combined with compressed air pulsations. The
resulting slurry is then passed through an inductive sensor to quantify the ferromagnetic
and non-ferromagnetic debris. This instrument has been applied to the external scavenge
filter fitted to the T56-A-14 and T-56-A-15 engines (powering the PBC and C130-H aircraft
respectively). Routine filter debris analysis is conducted at 150 hour intervals on these
Royal Australian Air Force (RAAF) engines. The advatages of this technique include less
time spent processing the filters, elimination of hazardous solvent exposure to staff and a
higher fidelity particle detection method.
File | Action |
---|---|
DSTO-TR-2773 Improvements to Filter Debris Analysis in Aviation Propulsion Systems.pdf | Download |
Comment On This Post