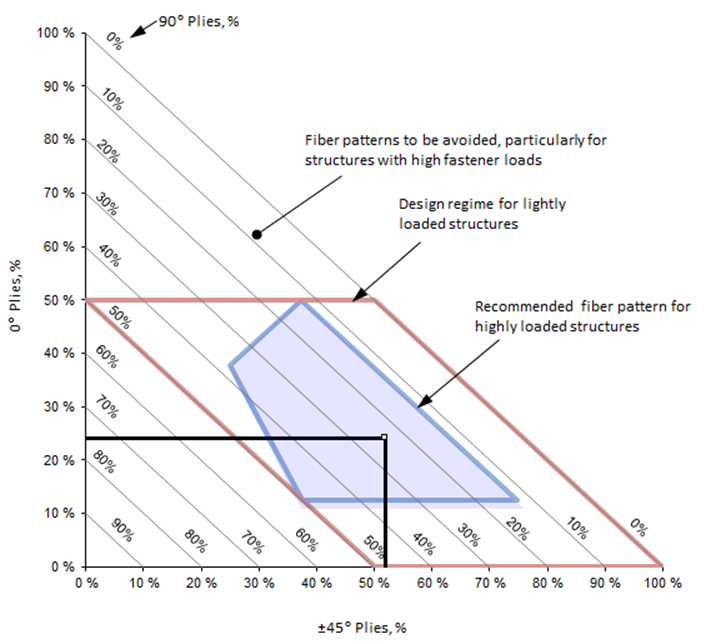
A version of this article first appeared in our free newsletter, to subscribe click here
An interesting technical issue came up this month that I posted on the Aircraft Stress Analysis LinkedIn group that I run. You can review the original post and the comments here: https://www.linkedin.com/feed/update/urn:li:activity:6701526665463414784
This is the original question:
“Bearing ‘yield’ of carbon fiber came up on a project yesterday. As long as the failure mode is not pull-out to the side of a sheet or flange, the bearing failure of carbon composite is non linear and progressive. For ultimate load cases can we ignore the ideal elastic load distribution between fasteners and just divide the total shear load by the number of fasteners?”
I had the unusual situation of a large fitting with multiple fasteners (12 bolts) in the center of a composite part – some distance from any panel edge. Most composite panel bearing stresses are based on a failure mode related to the edge of the panel.
I have gathered some useful data here: https://www.abbottaerospace.com/aa-sb-001/12-joints/12-2-mechanically-fastened-joints/12-2-4-mechanical-joints-in-composite-panels/
This shows the typical non linear response of a fastener in an ultimate bearing failure situation (Ref: http://www.abbottaerospace.com/wpdm-package/afwl-tr-86-3035)

And the effect of edge distance on the bearing strength (https://www.abbottaerospace.com/wpdm-package/arc-cp-1380-the-strength-of-bolted-joints-in-multidirectional-cfrp-laminates)

Should mean that in the center of panel we should see only bearing strength and the non linear nature of the bearing failure should give us some load redistribution between fasteners.
I got contacted by a good number of people publicly and privately (thanks to all of you!) and the consensus was that some redistribution would be reasonable in this situation.
I agree with this – especially as this is an arbitrary crash load case and is by nature a non service and conservative load condition.
This is for a foreign STC and so the opportunity to discuss with the relevant delegate is very limited (impossible!). So I will make sure this assumption is clear in the analysis and we will submit for review!
What do you think? Is this a reasonable assumption?
One recognized expert in composite joint design ,stressing, analysis etc is John Hart Smith –‘retired’ from Boeing via Mc Donnel and Douglas but still ‘on tap’ at 80 and producing new insights into composite buckling behaviour amongst other things – presently stranded in Australia from covid restrictions ( I could put you in touch if you liked ) –his know how is widely recognized and ,mostly, respected (except where his warnings prove true ..) Not sure WHEN you posted this but if you are still looking for input I will take it further. As a general comment I would think that bearing yield in carbon would be miniscule compared to interfastener strain or pin deformation even –design for bearing yield versus pin/bolt/rivet shear allows for some possible non catastrophic ‘survival’ after overload – in metal structures .(the bolting of the V tail attach bulkhead on HP sailplanes followed a flutter incident in which the holes elongated but the tail stayed on )