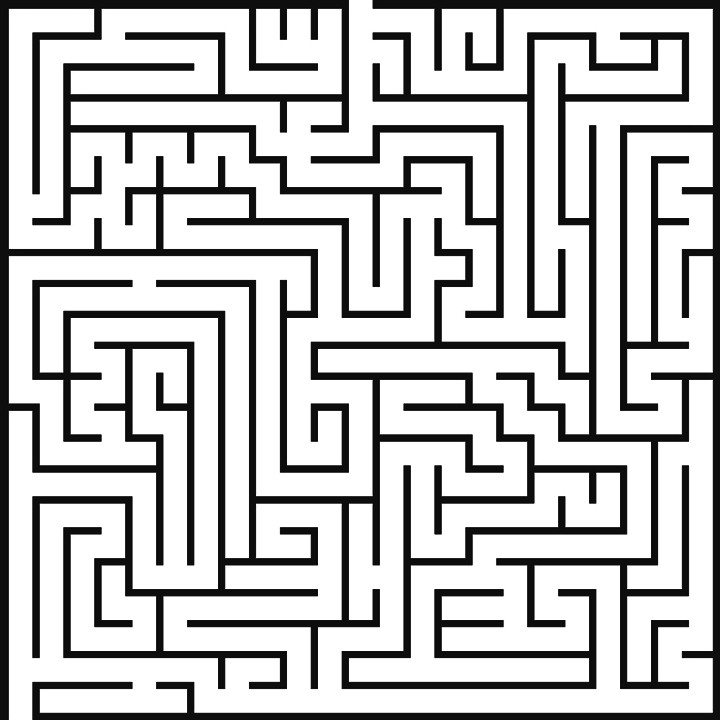
A version of this article first appeared in the May 2018 edition of our free newsletter, to subscribe click here
So you have engineered, built and flown your prototype aircraft. It has provided the metrics that you see looking for and the investors are happy. You now have to take all of the lessons learned from the prototype and develop your archetype – the production design. You also have to define the design to production design standards and develop your own in house processes. These processes have to be simple enough to enable you to build and sell at a profit but rigorous enough to ensure adequate quality and you qualify for the all important production certificate.
Most of my work is with the design engineers but as I work with more programs I have ended up getting drawn into the interface between design and manufacturing and then defining manufacturing processes.
This has all been very interesting, but during this expansion of my experience I have noticed a few important things.
- I did not realize how few of the engineers in the design groups I work with had ever picked up and read a process specification.
- Engineering teams that are good at producing prototype designs need a cultural shift in order to move into developing production designs
- Not all company management have no awareness of these issues, or see the impact of not tackling the issues.
There is a prevailing attitude in the prototype engineering group that manufacturing know what they are doing and it does not need to be defined on the face of the drawing. And that to define all of these obvious things on the face of the drawing is in some way insulting to manufacturing. In a practical sense this is true. An experienced machinist or layup technician knows what to do and how to do it to get a generally airworthy result. But they should not be responsible for deciding what is to be done. That is the job of the engineer.
The engineer should also know exactly how much definition is required to guarantee airworthiness and put no more than is required on the face of the drawing. This is maybe the hardest part for the engineer to get right. How much definition is too much definition?
So the drawing should define what is required for airworthiness. The process specification contains the approved manufacturing operations and consumable products that results in a finished part or assembly that is actually airworthy.
The process specifications need to be created by engineering and manufacturing working together – and this has to be done before the production design definition takes place.
At one of our clients this process is being handled ‘organically’ as we create drawings we define the required process on an as needed basis. This is not perfect and there are hiccups along the way. However, the engineers are getting involved in creating the process specifications and get a first hand view of how much thought and work is required – this is all good. How do the different classes and grades of anodizing affect hole diameter and the subsequent fit of a bushing?
In a perfect world we would just stop the entire program and create a complete set of process specifications and an entire quality system and the rest of the company would wait for us to finish. But I don’t think that is going to happen……
Comment On This Post