NASA-TM-2013-217967
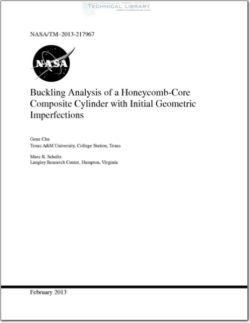
- Version
- 276 Downloads
- 5.43 MB File Size
- 1 File Count
- May 19, 2016 Create Date
- May 19, 2016 Last Updated
Buckling Analysis of a Honeycomb-Core Composite Cylinder with Initial Geometric Imperfections
The design of thin—walled cylindrical structures such as those in launch—vehicle barrel sections is
often controlled by the buckling response. Additionally, the buckling response of such thin-
walled cylinders is often sensitive to small geometric imperfections. To account for this
imperfection sensitivity during the design process, so-called knockdown factors are used in
design to reduce linear bifurcation—buckling buckling predictions to safe levels. The most used
source of knockdown factors for cylindrical shells is NASA SP-8007 [l], which is based on
empirical studies, was last updated in 1968, is considered overly conservative for many shell
designs [2], and does not consider the design space of many modern launch-vehicle shells.
NASA’s Shell Buckling Knockdown Factor (SBKF) project is developing new analysis—based
knockdown factors to update SP-8007 [3]. Several analysis methods can be used to predict
lower—bound buckling loads for cylindrical shells under axial compression. Incorporating
realistic manufacturing imperfection signatures in nonlinear buckling analyses is one approach
for developing analysis—based knockdown factors [4]. However, these imperfection signatures
are often not available during the design stage, before cylinders have been built. Therefore, other
analysis approaches may be needed to simulate geometric imperfections. In Ref. [5], the effects
of three other geometric imperfection types similar to those shown in Figure 1 were studied:
eigenmode imperfections, radial perturbation loads at the midlength of the cylinder, and single
stress-free dimple imperfections at the midlength of the cylinder. It was shown that the mode-
shape imperfection has a significant effect on the buckling load and the effective axial stiffness.
In contrast, it was shown that the radial perturbation and single dimple methods affect the
buckling load without significantly affecting the effective axial stiffness. The study confirmed an
earlier suggestion that the radial perturbation approach was a good method to develop improved,
less conservative shell—buckling design loads [6]. The SBKF project primarily uses the radial
perturbation method for determining lower-bound buckling knockdown factors [7].
File | Action |
---|---|
NASA-TM-2013-217967 Buckling Analysis of a Honeycomb-Core Composite Cylinder with Initial Geometric Imperfections.pdf | Download |
Comment On This Post