NASA-TM-102885
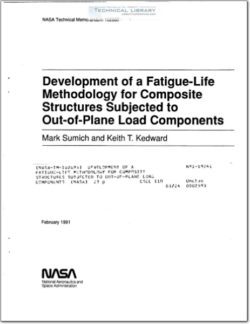
- Version
- 180 Downloads
- 1.19 MB File Size
- 1 File Count
- April 6, 2016 Create Date
- April 6, 2016 Last Updated
Development of a Fatigue-Life Methodology for Composite Structures Subjected to Out-of-Plane Load Components
The RSRA/X-Wing vehicle was a proof—of-concept stopped rotor aircraft configuration which
utilized a modified Rotor Systems Research Aircraft (RSRA) to examine the performance of a circu—
lation controlled four—bladed X-Wing rigid rotor (fig. 2). The X-Wing rotor may be operated in a
rotary wing mode much like a conventional helicopter or flown in a stopped rotor mode as fixed,
X-shaped wings. The lower, conventional wing is part of the basic RSRA and it permits the aircraft
to share the lift between the X—Wing rotor and the main wing or explosively jettison the X-Wing
rotor entirely and return to land safely. A complete description of the RSRA/X-Wing aircraft and a
review of the overall program are presented in reference 5. The program was terminated after the
initiation of rotorless flight testing due to insufficient funds.
A schematic of the X-Wing rotor system and a breakdown of the major precured blade compo-
nents are shown in figures 3(a) and 3(b). Each of the four 600-lb. rotor blades was constructed
almost entirely out of carbon fiber. The primary spar in each blade is a 260—lb laminated carbon fiber
I-beam called the flexbeam. The flexbeam attaches to the rotor hub at its root end and to the
outboard I-beam at its tip and carries the flatwise and edgewise bending moments and vertical shear
loads into the hub. The flexbeam has build-ups in flange thickness up to 2 in. thick at the root end to
reinforce the flexbeam where it is bolted to the hub, and tip end flange build-ups form wide, flat sur—
faces suitable for bonding into the outboard portion of the blade. Since the flexbeam is not bonded
along its length to the C-sections and is designed to be torsionally compliant, it is free to twist as the
rest of the bonded blade assembly is rotated around it to provide collective pitch control.
The material used was Celion G40-600 fiber impregnated with Narmco 5245C epoxy modified
bismaleimide resin to withstand the high—temperature compressed air that was internally channelled
down the leading and trailing edge ducts of each blade to provide aerodynamic circulation control.
All components were cured at 350° F, then post-cured at 400° F to provide the necessary high tem-
perature capability. The ducts would regularly be exposed to 320° F air which results in a 225° F
operating environment at the location of the flexbeam.
File | Action |
---|---|
NASA-TM-102885 Development of a Fatigue-Life Methodology for Composite Structures Subjected to Out-of-Plane Load Components.pdf | Download |
Comment On This Post