NASA-HDBK-5010
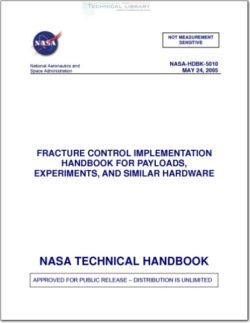
- Version
- 301 Downloads
- 5.15 MB File Size
- 1 File Count
- April 19, 2016 Create Date
- April 19, 2016 Last Updated
Fracture Control Implementation Handbook for Payloads, Experiments, and Similar Hardware
1. INTRODUCTION
To meet safety requirements for manned space flight systems as given in NASA-STD-
5007, NSTS 1700.78 and NSTS 1700.78 ISS Addendum, all payload and experiment hardware
flown on the NASA Space Shuttle or International Space Station must be assessed for fracture
control implementation. This handbook provides methodology and approaches for
implementation of fracture control on payloads or experiments flown on these vehicles and is
written to satisfy the intent of the applicable NASA fracture control requirements for payloads
and experiments delineated in References 1-9 in Section 4.
The guidance presented in this handbook reflects many years of implementation
experience related to fracture control assessment of hardware that has flown aboard the NASA
Space Shuttle. Experience has shown that, in general, relatively few parts or components in
payloads and experiments are truly "fracture critical". Some units or assemblies may have no
fracture critical parts. The guidance reflected in this handbook aids in classification of parts and
helps reduce the number of parts that, because of lack of definition, could be classified fracture
critical unnecessarily. Fracture critical designation requires special considerations and
treatment for the respective part. This is absolutely necessary on parts, whose failure is
catastrophic, but can become resource consuming and potentially schedule significant if parts
are classified fracture critical in a casual manner.
A viable fracture control program relies on design, analysis, non-destructive evaluation,
and tracking of fracture critical hardware. It is expected that flight hardware will be consistent
with aerospace standards, practices, and quality. It is beyond the scope, or intent, of this
document to address technical or quality disciplines that should already exist and be in place
irrespective of fracture control. Fracture control is imposed and required to enhance safety of
manned space flight systems. Fracture control programs can significantly supplement properly
designed, high quality hardware with additional assurance against catastrophic structural
failures caused by unexpected and/or undetectable flaws. Fracture control is not intended to
compensate for poor design, analytical errors, misuse, or poor quality. Although fracture control
can be effective in adding assurance of mission success, it is not specifically required for that
purpose in References 1-9.
Since fracture control deals with what might happen in the event that crack propagation
leads to structural failure, reasonableness and credibility must prevail. Many bad things can be
imagined as a result of chained, unlikely events. Consequently, those who do fracture control
and those who judge it must put some restraint on their imaginations and temper them with the
likelihood that the events under consideration have a reasonable chance of occurring.
Basic assumptions that underlie fracture control implementation include:
a. All individual structural parts contain flaws or crack-like defects. Minimum life of the
part may be determined by considering one and only one flaw in the most critical area of the
part and in the most unfavorable orientation.
File | Action |
---|---|
NASA-HDBK-5010 Fracture Control Implementation Handbook for Payloads, Experiments, and Similar Hardware.pdf | Download |
Comment On This Post