NASA-GD-ED-2205
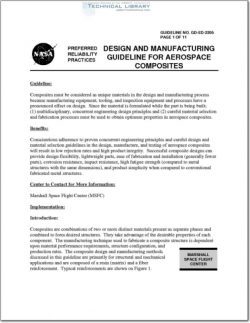
- Version
- 336 Downloads
- 107.43 KB File Size
- 1 File Count
- August 18, 2016 Create Date
- August 18, 2016 Last Updated
Design and Manufacturing Guideline for Aerospace Composites
The success of a composite program is dependent upon establishing material properties early in
the program. Establishing an accurate and reliable material property data base is one of the most
important steps toward achieving a functional design. Experience indicates that the basic
material allowables of a specific composite product should be determined utilizing the
manufacturing facilities where production will take place prior to finalizing design. The
preferred process should approximate the following: (1) define environmental and performance
requirements; (2) review available materials against requirements to determine the family of
material to be used; (3) determine materials; (4) determine materials allowables using material
processed at the intended manufacturer; (5) proceed with design based on known material
GUIDELINE NO. GD-ED-2205
PAGE 3 OF 11
DESIGN AND MANUFACTURING GUIDELINE FOR
AEROSPACE COMPOSITES
allowables; (6) test geometric configurations (i.e., special joints, specific contours, special ply
layups, etc.); (7) along with nondestructive evaluation (NDE), use destructive evaluation to
determine voids, ply dropoff, resin rich areas, etc., during initial manufacturing process
development; (8) begin manufacturing production. Typical mechanical and impact damage
properties of selected composites are shown in Tables 1 and 2.
Recommended Design and Analysis Guidelines for Composites:
During the concept definition phase of the composite part design cycle, all of the critical design
parameters are established. Geometric constraints and material considerations are outlined in
order to establish the amount of design flexibility allowable. Maximum loads, both mechanical
and thermal, are estimated. Weight, cost, and producibility concerns should be considered at this
juncture. These factors should then be weighted and balanced to produce an initial design
concept. For example, thermal material limitations should be balanced against cost and
producibility concerns to select the appropriate composite material. Likewise, the layup of the
laminate should be chosen considering not only the desired load capability, but also the thermal
environment. High heat transfer areas could be cooled by using additional plies to act as a heat
sink. These two factors in turn are offset by weight considerations. Several preliminary analysis
and sizing tools can be used at this stage. PANDA, an elastic—plastic composite shell
optimization program, is used in the analysis of stiffened panels. For flat composite panels,
PASCO is sometimes used for preliminary sizing. The use of a Computer Aided Design (CAD)
package is highly desirable in drawing the initial configuration.
The configuration is then subjected to stress analysis. Depending on complexity, the part may
be subdivided into subcomponents for separate analysis. If required, a structural computer
model may be generated. For most parts, a finite element model is generated using
PDA/PATRAN and the surface definitions from the CAD drawing.
File | Action |
---|---|
NASA-GD-ED-2205 Design and Manufacturing Guideline for Aerospace Composites.pdf | Download |
Comment On This Post