NASA-565-PG-8700-2-1B
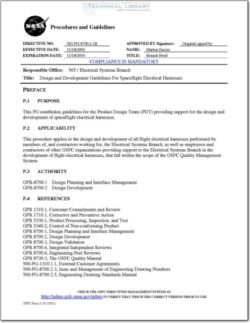
- Version
- 101 Downloads
- 119.07 KB File Size
- 1 File Count
- May 14, 2016 Create Date
- May 14, 2016 Last Updated
Design and Development Guidelines for Spaceflight Electrical Harnesses
PREFACE
P.1 PURPOSE
This PG establishes guidelines for the Product Design Team (PDT) providing support for the design and
development of spaceflight electrical harnesses.
P.2 APPLICABILITY
This procedure applies to the design and development of all flight electrical harnesses performed by
members of, and contractors working for, the Electrical Systems Branch, as well as employees and
contractors of other GSFC organizations providing support to the Electrical Systems Branch in the
development of flight electrical harnesses, that fall within the scope of the GSFC Quality Management
System.
2. Initial Planning
2.1. The lead engineer develops the design plan, which contains a high level description of the
electrical harness to be developed, key support personnel, a budget, and a schedule for review and
approval by the customer. The plan should include adequate contingencies for completion of the
design and development activity within the resources negotiated in the Customer Agreement
and/or SOW (see GPR 1310.1, Customer Commitments and Review and/0r 500-PG—1310.l,
External Customer Agreements). A project or instrument manager may request this design plan
information be documented in a formal Implementation Plan for the electrical subsystem. Other
approaches may be to have the design planning documentation combined with other discipline
inputs and consolidated into a Project Plan, or the design planning documentation may be a part of
several individual project documents. Regardless of the approach, the design planning
documentation is a quality record and shall be maintained per the applicable configuration
management plan for this design and development activity.
2.2. The lead engineer, with assistance from line management, ensures that the PDT is composed of
individuals, civil servants and/0r contractors as necessary, with the required discipline skills.
3. Requirements Definition
The lead engineer supports the generation of a requirements document from the design inputs. It may be
necessary for the PDT to perform various analyses in order to derive lower level design requirements
from the top-level design inputs. These top level and derived requirements shall be documented,
reviewed for adequacy and consistency with relevant NASA and GSFC standards, and signed off by the
lead engineer and the customer. The requirements document shall be maintained per the applicable
configuration management plan.
File | Action |
---|---|
NASA-565-PG-8700-2-1B Design and Development Guidelines for Spaceflight Electrical Harnesses.pdf | Download |
Comment On This Post