DOT-FAA-AR-03-74
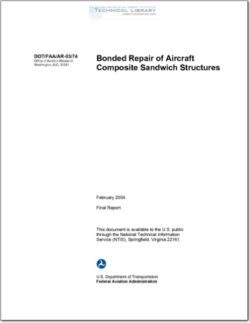
- Version
- 340 Downloads
- 3.80 MB File Size
- 1 File Count
- March 24, 2016 Create Date
- March 24, 2016 Last Updated
Bonded Repair of Aircraft Composite Sandwich Structures
The use of composite materials in aircraft structural components has increased in the past few
decades as a result of the many advantages they offer compared to metals. Composite airframe
structures, unlike traditional metal structures, have high strength and stiffness to weight ratios,
have a good fatigue resistance, and are less prone to deterioration caused by corrosion and
cracking. Nevertheless, they are more sensitive to other types of damage, mainly impact damage
that can cause disbonding, delamination, and internal crushing. Therefore, to improve the
performance of composite aircraft structures in the long run and take advantage of their many
benefits, one should first ensure that these structures are durable, repairable, and maintainable
Composite structures are primarily damaged by lightning strikes, tool drops, service vehicle
collisions, hail, runway debris, and birds. Other sources of damage include erosion, abrasion,
manufacturing defects, excess heat exposure, and fluid infiltration. Therefore, the extent of the
damage determines whether the component needs to be repaired or replaced. In most cases,
replacing the entire part is not economically feasible; thus, repairing it is the only viable solution.
Furthermore, since the time constraint is an issue, repairs must be performed as quickly as
possible so that the aircraft can be returned to service as soon as possible.
When designing a composite repair, several factors must be considered to ensure the repair’s
effectiveness and structural integrity. These factors include stiffness, strength, stability,
operating temperature, durability, and aerodynamic smoothness [2].
The stiffness of the repair should match, as close as possible, the stiffness of the parent structure.
A repair that is stiffer than the parent structure would attract more load to the repaired region,
possibly causing it to exceed its allowable strength. On the other hand, a repair with a lower
stiffness than the parent structure would divert the load from the repair, possibly causing it to
overstress the parent structure.
When considering the strength of a composite repair, one should try to match the strength and
stiffness of the parent structure. However, this is not always possible unless the same materials
and processes are used. In most cases, a different repair material is used. Therefore, while
ensuring that the stiffnesses are matched, a positive strength margin of safety should be achieved.
File | Action |
---|---|
DOT-FAA-AR-03-74 Bonded Repair of Aircraft Composite Sandwich Structures.pdf | Download |
Comment On This Post