AGATE-WP3.3-033048-117
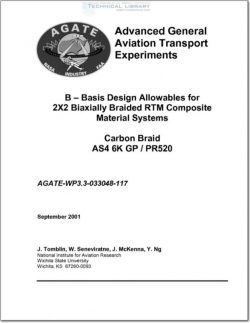
- Version
- 297 Downloads
- 5.29 MB File Size
- 1 File Count
- August 8, 2016 Create Date
- August 8, 2016 Last Updated
B-Basis Design Allowables for 2X2 Biaxially Braided RTM Composite Material Systems - Carbon Braid AS4-6K-GP-PR520
The Advanced General Aviation Transport Experiments (AGATE) consortium is an
industry-university—government partnership initiated by NASA to create the technological
basis for revitalization of the United States general aviation industry. It was founded in
1994 to develop affordable new technology as well as the industrial standards and
certification methods for composite airframe, cockpit, flight systems and airspace
infrastructure for Federal Aviation Regulations (FAR) Part 23 aircraft. The composite
material properties contained within the document were generated under Work Package
3 : Integrated Design and Manufacturing Methods.
Although AGATE was focused towards the small general aviation aircraft (Part 23), the
test methods and results contained in this document are consistent with MIL-HDBK-17-
1E,2D,3E - Military Handbook for Polymer Matrix Composites. All material, specimens,
fixtures and test results contained within this document were traceable and conformed by
the Federal Aviation Administration (FAA) as part of the AGATE effort. It should be
noted that before application of the basis values presented in this document to design,
demonstration of the ability to consistently produce equivalent material properties as that
evaluated during this program should be substantiated through an acceptable test
program.
The test methods and results described in this document are intended to provide basic
composite properties essential to most methods of analysis. These properties are
considered to provide the initial base of the “building block” approach. Additional coupon
level tests and subelement tests may be required to fully substantiate the full-scale
design.
The mechanical behavior of braids hinges upon the fiber geometry. The geometry of a
periodic textile can be conveniently illustrated in terms of a repeating pattern, referred as
the Repeating Unit Cell or RUC (Figure 1.5.1).
Braided preform is produced in a tubular shape. The braid angle is the angle of the
braided yarns measured relative to the axis parallel to the axis of the tube (braid
direction). The diameter of the resulting braid is usually defined at the braid angle of
145°. By stretching or compressing the braid, the braid angle can be changed between
the tensile and compressive jam angles.
File | Action |
---|---|
AGATE-WP3.3-033048-117 B-Basis Design Allowables for 2X2 Biaxially Braided RTM Composite Material Systems - Carbon Braid AS4-6K-GP-PR520.pdf | Download |
Comment On This Post